Dělení železných a neželezných kovů je nedílnou součástí výrobních procesů. Na trhu lze nalézt velké množství technologických řešení, která se svými rozličnými vlastnostmi hodí pro rozdílné požadavky zákazníků. K velké a v průmyslu značně rozšířené metodě dělení materiálu řadíme dělení termické, jež využívá tepelnou energii. Tepelný zdroj se u jednotlivých metod liší, avšak jedno mají společné – koncentraci tepelné energie do místa řezu. Ve srovnání s konvenčními technologiemi tato metoda vyniká vysokou rychlostí řezání, přesností nebo možností dělit materiály jinak nedělitelné či jen s velkými obtížemi.
KYSLÍKOVÉ ŘEZÁNÍ
Kyslíkové řezání patří k nejstarším metodám tepelného dělení materiálů. Někdy je označováno jako autogenní nebo řezání plamenem. Proces lze přirovnat k hoření. Je tedy nutné splnit všechny podmínky tzv. trojúhelníku hoření: hořlavá látka (dělený materiál), oxidační prostředek (kyslík) a iniciační zdroj (plamen, ohřátý dělený materiál). Povrch děleného materiálu se nahřeje pomocí plamene z autogenního hořáku na zápalnou teplotu. Po dosažení dostatečné teploty povrchu dělené součásti a otevření přívodu řezacího kyslíku dojde ke spalování železa. Vznik exotermické reakce mezi proudem řezacího kyslíku a děleného materiálu produkuje potřebnou tepelnou energii pro spalování řezaného dílu a udržení procesu řezání. Řezná spára (obr. 1) vzniká díky působení tlakové energie kyslíku na roztavené oxidy kovů, které jsou tak vyfukovány.
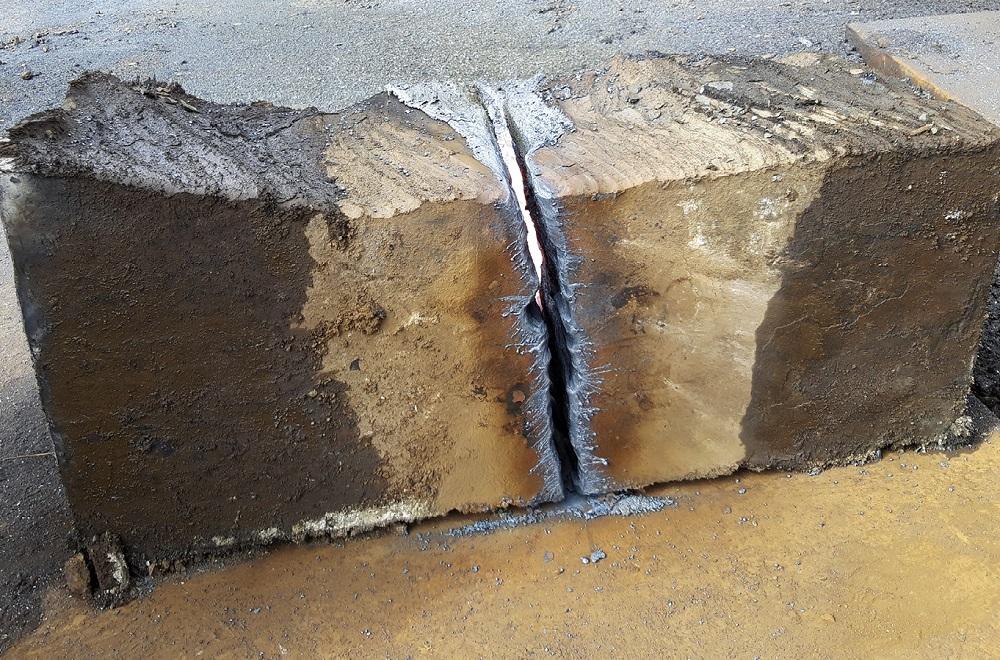
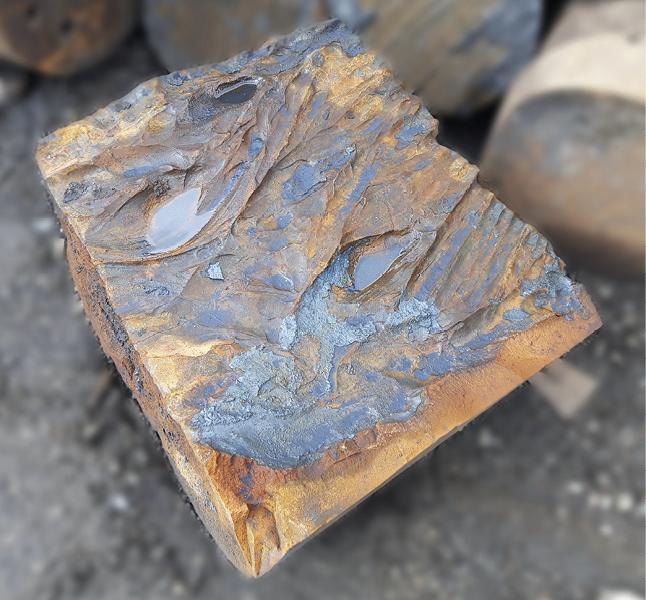
Touto technologií mohou být řezány nelegované a nízkolegované oceli, protože díky svému chemickému složení obsahují omezené množství legujících prvků. Při požadavku na dělení materiálu s omezenou řezatelností, jako jsou například litiny, vysokolegované oceli či neželezné kovy, je třeba kombinovat kyslíkové řezání se železným práškem.
Metodou kyslíkového řezání lze zpracovat materiály přibližně do tloušťky 300 mm, při použití profesionálních hořáků i více jak metr. Je však nutné brát v úvahu velké tepelné ovlivnění děleného materiálu a nepravidelnou plochu řezu (obr. 2).
Omezujícím prvkem kyslíkového řezání je především řezaný materiál, jenž musí splňovat následující podmínky řezatelnosti:
- Zápalná teplota musí být nižší než jeho teplota tavení.
- Teplota tavení oxidů kovu musí být nižší než teplota tavení řezaného kovu.
- Tvořící se oxidy musí být dostatečně tekuté.
- Generované teplo vzniklé spalováním musí eliminovat tepelné ztráty.
PLAZMOVÉ ŘEZÁNÍ
Plazmové řezání je další nekonvenční metoda termického dělení využívající vysoké teploty a výstupní rychlosti plazmového paprsku. K vytvoření plazmového oblouku dochází po ionizaci technického plynu proudícího kolem elektrody plazmového hořáku. Paprsek plazmatu díky své vysoké energetické hustotě po dopadu na materiál způsobuje velmi rychlé lokální natavení a odpar materiálu. Zbylá energie plazmového paprsku, která není převedena na energii tepelnou, díky svému vysokému kinetickému potenciálu vyfukuje taveninu z procesu řezu, čímž vzniká řezná spára.
Výhodou plazmového řezání je možnost použití nejen pro nelegované a nízkolegované oceli, ale i pro řezání korozivzdorných, vysokolegovaných a vysokouhlíkových ocelí a zároveň i neželezných kovů či litin. Také tepelné ovlivnění děleného materiálu je menší. Maximální řezná tloušťka se odvíjí od výkonu zdroje, přesto v praxi se plazmové řezání používá převážně do tloušťky 50 mm.
LASEROVÉ DĚLENÍ
![]() |
|
Obr. 3 – Laserové řezání. |
Poslední, ale dnes již velmi rozšířenou technologií pro dělení materiálu, je laser, respektive laserový paprsek (obr. 3). Jde o světelný paprsek, tedy proud fotonů o jednotné vlnové délce. Při interakci laserového paprsku s povrchem děleného materiálu dochází k přeměně vysoce koncentrované světelné energie na energii tepelnou, což se projevuje prudkým ohřevem děleného materiálu v místě řezu. Natavený materiál je opět pomocí dynamického účinku proudu technického plynu odstraněn z řezu. Jako řezný plyn se používá kyslík nebo dusík. Nejčastěji se laserové řezání využívá pro tloušťky plechů do 15 mm, ale na dnešním trhu lze nalézt stále více vysokovýkonných laserů, které umožňují řezat materiály i větší tloušťky, než je 25 mm.
Při použití kyslíku se jedná o tzv. oxidační řezání, jež je ve své podstatě velmi podobné kyslíkovému, tedy autogennímu řezání a používá se pro nelegované či nízkolegované materiály větších tlouštěk. Dělený materiál je v místě řezu nataven pomocí laserového paprsku na zápalnou teplotu a následně částečně spálen energií vznikající z exotermické reakce při styku s proudem kyslíku. Důležitým prvkem je i samotná čistota kyslíku, neboť ovlivňuje výslednou řeznou rychlost. Použití kyslíku Oxycut o čistotě 3.5 (99,95 %) vede k nárůstu získané energie z exotermické reakce, a tedy i vyšší řezné rychlosti (obr. 4).
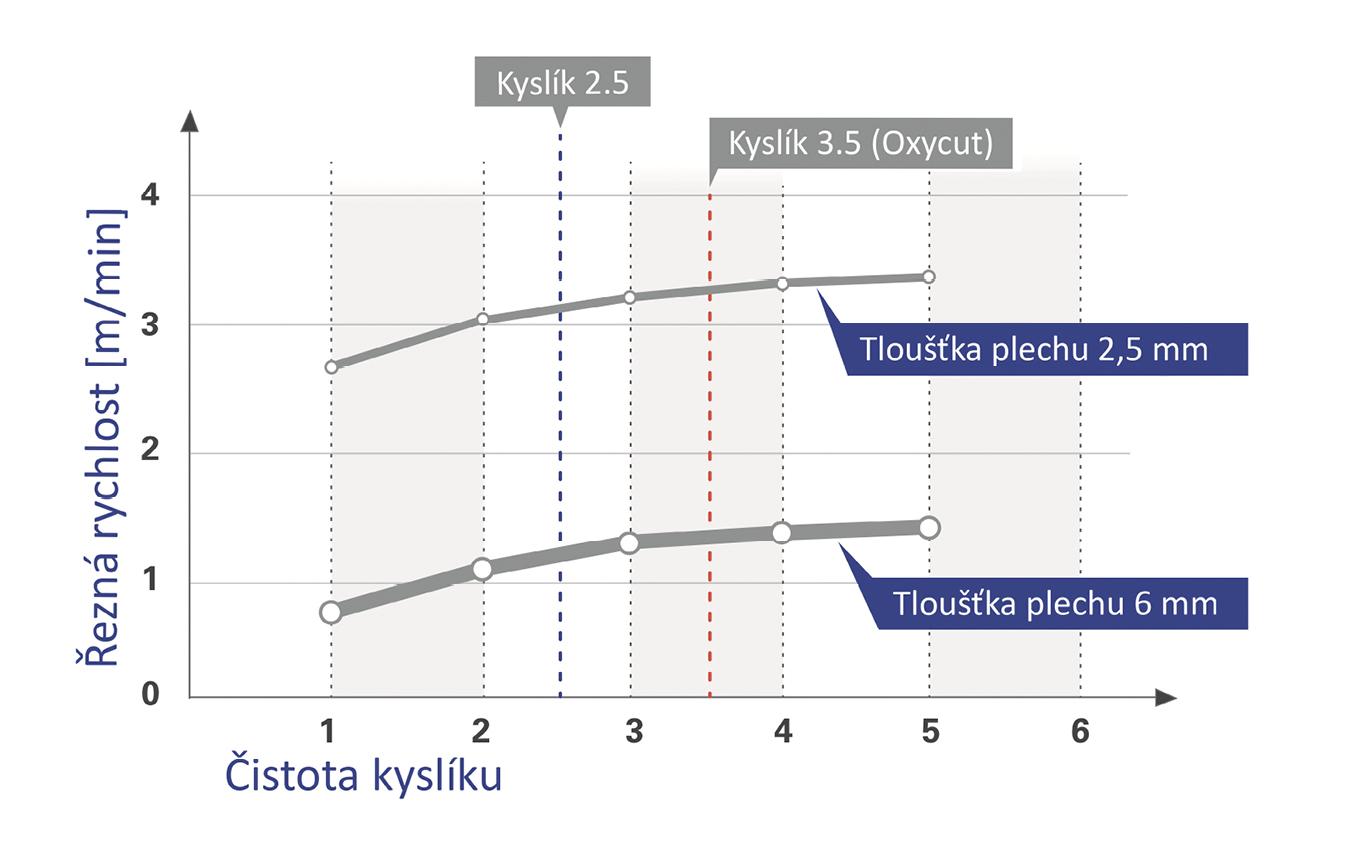
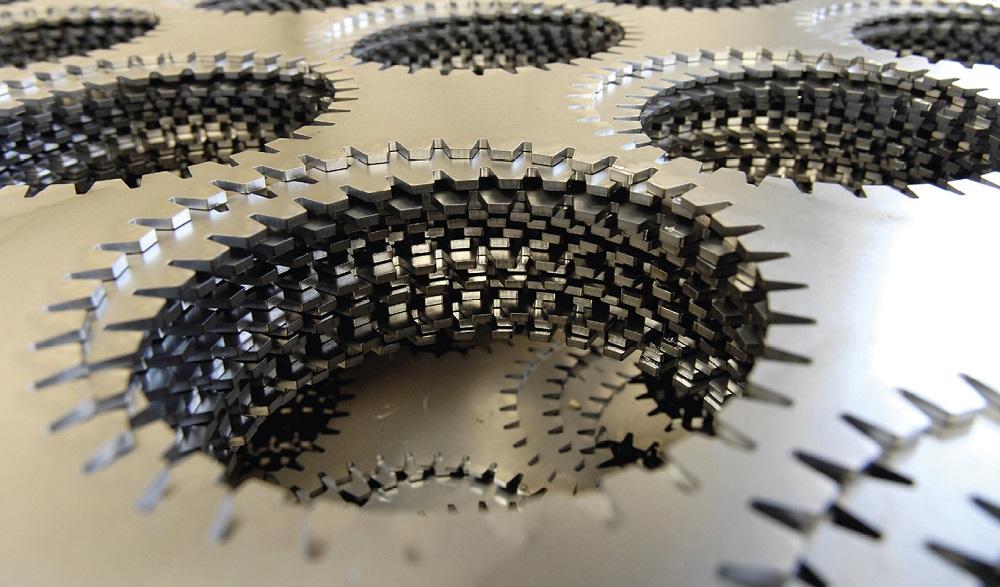
Dalším možným řezným plynem je dusík. Ten se využívá pro materiály nelegované, legované a neželezné kovy. Označuje se jako tavné řezání. Princip tavného řezání je velmi podobný oxidačnímu, ale s tím rozdílem, že z důvodu použití inertního plynu nedochází k exotermické reakci. Zároveň je využíváno násobně většího tlaku řezného plynu, který může dosahovat i více jak 20 barů. Dusík, nejčastěji čistoty 5.0 (99,999 %), nereaguje s řezaným materiálem, což se projevuje kovově lesklými řeznými plochami bez oxidů (obr. 5).
TECHNICKÉ PLYNY A VHODNÉ ZÁSOBOVACÍ SYSTÉMY
![]() |
|
Obr. 6 – Kryogenní zásobník Foto: Messer Technogas |
U každé z výše popsaných technologií je nutné zabezpečit dodávky technických plynů. Z kvalitativního hlediska se sleduje především čistota plynů, kterou je pro dosažení nejlepších výsledků výpalků vždy dobré dodržovat. Zdrojem těchto plynů mohou být při malé spotřebě tlaková lahev nebo svazky tlakových lahví. Pro větší spotřebu je z hlediska usnadnění manipulace, zvýšení bezpečnosti provozu a v neposlední řadě finančních úspor výhodné použití kryogenních zásobníků (obr. 6). O ideální volbě zdroje plynu plynu je vhodné diskutovat s dodavatelem technického plynu, který na základě svých zkušeností dokáže vyhodnotit nejlepší způsob zásobování.
BUDOUCNOST TERMICKÉHO DĚLENÍ
Termické dělení má díky kyslíkovému řezání hluboké kořeny v historii nekonvenčního dělení materiálů. I přes tuto skutečnost vývoj v tomto odvětví nijak neutichá a stále se setkáváme s evolučními řešeními, které umožňují dosažení vyšší produktivity a kvality při dělení materiálů za udržení minimálních výrobních nákladů.
Autor:
Ing. Jan Šplíchal, IWE, aplikační inženýr svařování a dělení materiálů ve společnosti Messer Technogas. Specialista v oblasti technických plynů pro laserové aplikace a svařování. Spoluřešitel projektu AdMan Tool.