Pro výrobu designových panelů kýlu se vytvořilo přes 18 000 výrobních a kompletačních výkresů
Architektonický návrh Masaryčky od Zahy Hadid je unikátní nejen designem obvodového pláště, ale představoval také velkou výzvu pro realizaci celé fasády, kterou realizovala společnost Sipral. Z velké členitosti a tvarové pestrosti s mnoha křivkami vyplývala jednoznačně potřeba řešit nadstandardní objem atypických detailů a vzájemných návazností různých typů konstrukcí fasády. Na celém obvodovém plášti je osazen velký počet originálních fasádních dílů, jež se neopakují, proto byly vyráběny jako jedinečné kusy. Atypičnost a členitost pláště se odrážela ve vysokých nárocích nejen na projekční práce, ale také na samotnou výrobu, montáž i dodavatelský řetězec.
Společnost Sipral zahájila práce na projektu technickou přípravou a zpracováním projektové dokumentace v srpnu 2021. Montáž konstrukcí obvodového pláště přímo na stavbě pak byla zahájena na začátku dubna 2022.
TECHNICKÉ ŘEŠENÍ A REALIZACE OBVODOVÉHO PLÁŠTĚ
Zadávacím dopisem v srpnu 2021 od klienta Penta Real Estate jsme kontinuálně navázali na předešlý proces výběrového řízení, kde již byla koncepce obvodového pláště detailněji projednávána před samotným rozhodnutím klienta o dodavateli opláštění.
V návaznosti na projektovou dokumentaci zadání jsme v počátku projektu navrhli některé úpravy technického řešení. Jednalo se zejména o návrh vlastního unikátního řešení kýlu a o změnu původní technické koncepce opláštění hlavních fasád nad úrovní parterů, tedy od 3. NP výše na řešení konceptem modulové fasády, jež tvoří podstatný rozsah opláštění objektu.
O takto rozsáhlém obvodovém plášti s jedinečnou architekturou bychom mohli napsat mnoho stran o technickém řešení, přípravě a realizaci každé jednotlivé konstrukce. Nicméně naším záměrem je především představit základní průřez dodávaných konstrukcí s jejich specifiky.
MODULOVÁ FASÁDA A PROSTOROVÉ POHLEDOVÉ LAMELY
Instalace fasádního modulu s osazenými prostorovými tvarovkami (lamelami) a obkladem GRC. Koncept modulové fasády umožnil v předstihu vyrábět kompletní fasádní dílce v kontrolovaném prostředí výroby a na moduly přímo ve výrobě osadit jak pohledové GRC desky (sklovláknobeton), tak také prostorové vodorovné lamely. V modulech jsou osazena ven výklopná okna s vnější pohledovou plochou tvořenou GRC deskou, pod níž je z důvodu zlepšení tepelnětechnických parametrů osazen VIP panel (vakuově izolační panel).
Takto připravené kompletní fasádní moduly byly následně instalovány při montáži pomocí jeřábu na předem připravené kotvení bez potřeby lešení. Osazením fasádního modulu jsme jedním krokem uzavírali objekt a zároveň s modulem osazovali i pohledové prvky.
Významnou roli v samotné realizaci hrál rovněž fakt, že vodorovné prostorové pohledové lamely „obíhají“ okolo objektu a vzájemně na sebe navazují.
Horizontální lamely pak v přední části, po obou podélných stranách směrem ke kýlu, navazují přes obloukové tvarovky a tzv. „výhybky“ na vertikální lamely, které přecházejí až nad úroveň atiky do tzv. „koruny“.
Pohledové prvky navíc probíhají přes různé typy konstrukcí s odlišným postupem montáže, což kladlo vysoké nároky již od úrovně projektování – bylo potřeba převést zadané plochy do 3D programu Solidworks a Catia, ve kterém se následně modelovaly jednotlivé části fasád, a také přes vhodně zvolené technologické postupy výroby a montáže na stavbě s důrazem na přesnost zaměření i samotné montáže.
Pohledové lamely i obloukové dílce byly vyrobeny z hliníkového plechu tloušťky 3 mm. Na vnitřní, nepohledové straně, jsou lamely vyztuženy žebry, která zajišťují jejich statickou a tvarovou stabilitu.
Povrchová úprava je provedena práškovým lakem. Dominantní linky lamel pak tvoří pásky ze zlatě eloxovaného hliníkového plechu ve shodném odstínu, jako je kýl a podhledy.
Ve spodní části, kde fasády přecházejí na zlaté podhledy, jsou lamely fasády řešeny nejen se zlatým páskem, ale i se zlatou spodní polovinou lamely, která tak opticky vytváří plynulý přechod fasády na zlaté podhledy.
Na fasádu jsou prostorové pohledové lamely osazeny přes bajonetové čepy, jež umožňují potřebnou dilataci nezávisle na fasádě.
DIAGONAL BAYS
Plocha modulových fasád je na podélných stranách ze severu a z jihu vždy zhruba v polovině každého objektu „protnuta“ ustupujícími fasádami, tzv. Diagonal Bays.
Tato část je řešena fasádou typu sloupek–příčník. Samotný šikmý přechod mezi plochou modulové fasády a ustoupeným prosklením Diagonal Bays je vyřešen nosnou ocelovou konstrukcí osazenou mezi jednotlivá podlaží. Ocelová konstrukce slouží především jako nosný prvek pro vnější a vnitřní obklady a k napojení navazujících fasád. Ocelová konstrukce je doplněna o potřebnou tepelnou izolaci a hydroizolační uzavření.
Na straně z interiéru je osazena kapotáž z pohledových lakovaných plechů se skrytým uchycením ke konstrukci.
Z exteriéru je prosklení Diagonal Bays lemováno GRC deskami (sklovláknobeton) osazenými na šikmých bočních plochách ustupující konstrukce. Ze stejného materiálu je tvořen i podhled a ve spodní části probíhající tvarovky, které navazují na průběžné hliníkové lamely fasády. Napojení mezi šikmými a vodorovnými plochami GRC obkladů na jejich spodní straně v každém podlaží je řešeno rovněž z materiálu GRC jako prostorově tvarované dílce, tzv. „filety“, které vytvářejí plynulý přechod mezi těmito konstrukcemi.
FASÁDY PRVNÍHO A DRUHÉHO NADZEMNÍHO PODLAŽÍ
Ve spodní části obou objektů, na úrovni 1. NP a 2. NP, probíhají prosklené fasády zasklívané na stavbě do předem namontovaného fasádního rastru.
V nárožích je zasklení řešeno obloukovými skly, na západní straně fasády, pod kýlem a na východní straně vždy osazením více ohýbaných skel vedle sebe.
Fasády vstupního lobby a fasáda pod kýlem mají spáry mezi skly tmelené, ostatní části těchto fasád pak mají spáry kryté přítlačnými lištami.
Zasklení fasád je řešeno trojskly, kdy největší skla mají celkovou tloušťku 80 mm a jejich váha, při výšce zhruba 5 m, přesahuje 1 300 kg. Pro zasklívání bylo nutné použít savku (vakuový manipulátor) s nosností 2 t a pro zasklení obloukových skel pak speciální savku se 44 nosnými talíři.
Vysokému zatížení fasád odpovídal i statický návrh, který mimo jiné zahrnoval výrazně zesílené kotvení a použití výztuh nosného rastru.
PODHLEDY
Přechod mezi ustoupenými fasádami 1. a 2. NP a plochou modulové fasády je řešen podhledem z hliníkových kazet tloušťky 3 mm s povrchovou úpravou zlatou eloxáží. Podhledy v této úrovni probíhají nejen na podélných stranách objektu, ale také v místě mezi objekty (centrální prostor Rotated Plazza), v němž jsou obě strany podhledů propojeny, stejně tak i na východní straně objektu.
Na západní straně, směrem k náměstí u Masarykova nádraží, pak zlatý podhled plynule přechází do prostorové konstrukce zlatého kýlu.
Zlaté podhledy jsou na objektu osazeny i na jednotlivých terasách.
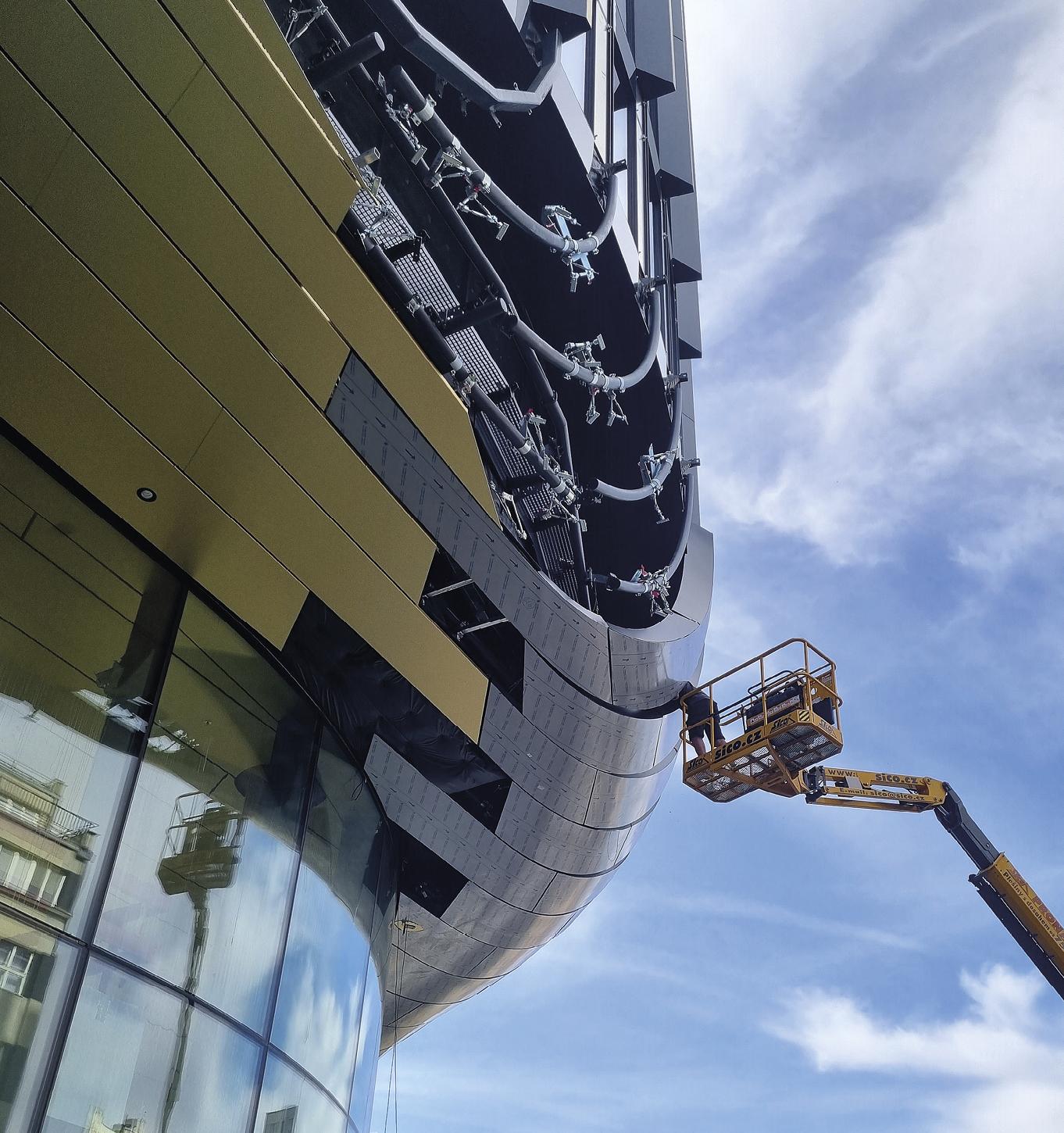
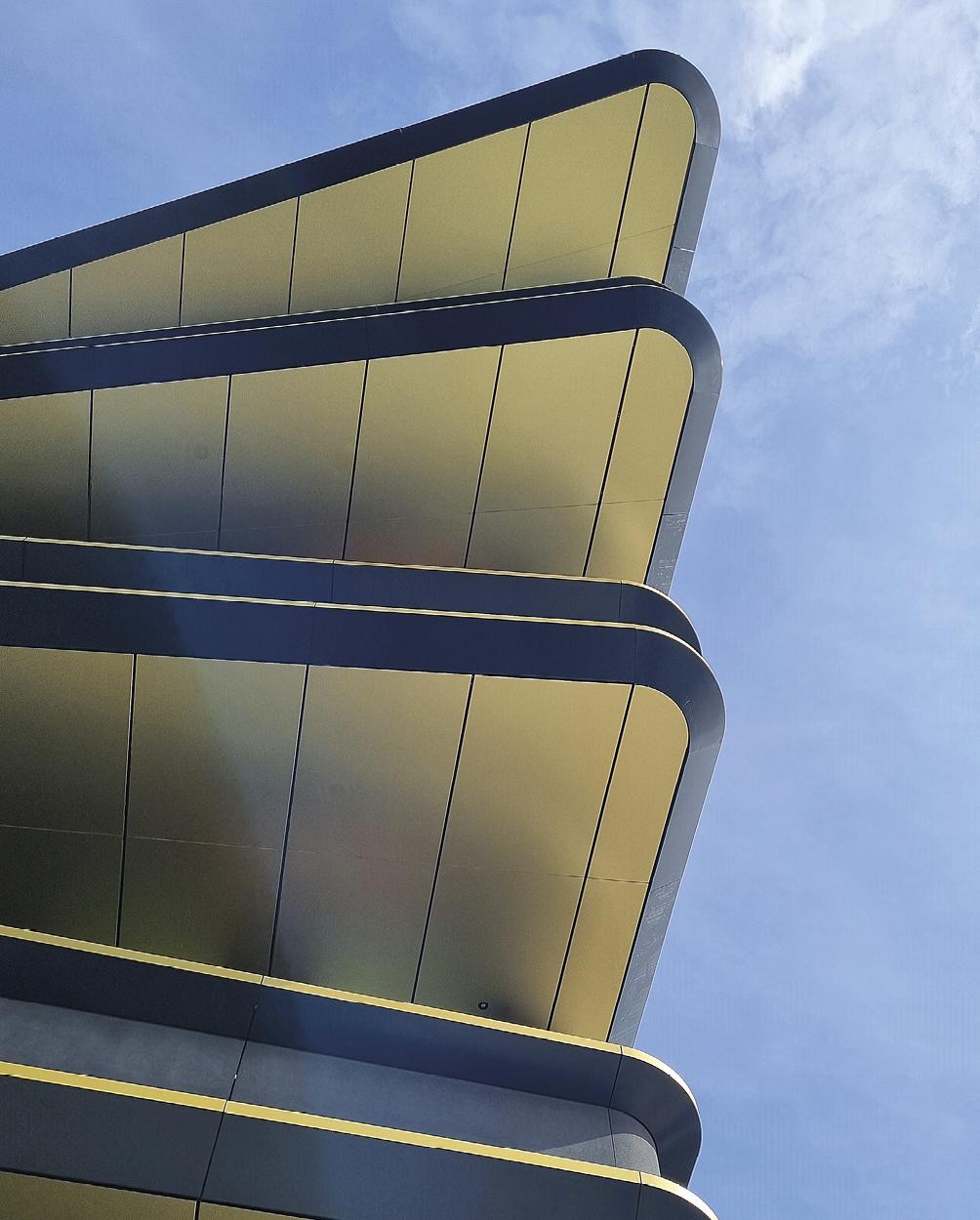
JEDNOTLIVÉ FÁZE REALIZACE
Atypičnost a členitost opláštění kladly vysoké nároky na všechny procesy od přípravy až po montáž na stavbě.
Při zpracování technických návrhů a projektové dokumentace jsme využívali koncept kombinace 3D a 2D projektování. Správa výrobní dokumentace včetně kusovníků probíhala v interním informačním systému Sipralis.
Při projektování se nejednalo jen o zpracování projektové dokumentace, ale také o promýšlení postupů ve výrobě a na montáži tak, aby vše do sebe zapadalo a byly eliminovány budoucí kolize, o které u takto složitých projektů není nouze.
Náročnost a druhovost tvarových prvků znamenala vytvářet samostatnou dokumentaci pro každý originální díl a vést intenzivní komunikaci s výrobou a subdodavateli nad technologií výroby, ale také nad způsobem balení, aby nedocházelo k poškozování výrobků při přepravě a manipulaci.
Zvolené postupy pak byly ověřovány na vybraných vzorových výrobcích ve skutečné velikosti. Mnohdy bylo nutné provést korekci zvoleného řešení a vzorové výrobky vyrábět opakovaně, dokud nebyla jistota, že postup je správný. Toto nebylo však možné realizovat pro každý jednotlivý tvar, protože mnoho dílů je jedinečných. Například u obloukových tvarovek, a zvláště pak přechodových „výhybek“ se odladily principy výroby, ale tvary, respektive rádiusy se u jednotlivých dílů odlišovaly.
Obdobným způsobem se připravovaly postupy pro montáž na stavbě.
Klíčové bylo nastavení logistiky celého projektu, což zahrnovalo i principy komunikace uvnitř týmu, ale především se všemi dodavateli o časovém plnění dodávek, kontrole kvality nebo řešení neshodných výrobků.
ZAJÍMAVOSTI Z REALIZACE FASÁDY
- Prostorových hliníkových lamel včetně obloukových dílů, mimo kýl, je na projektu použito více než 2 200 ks.
- Na kýlu je osazeno 265 ks unikátních zlatých panelů.
- Pohledové zlaté pásky dosahují celkové délky téměř 6 km.
- Celkem je na objektu osazeno zhruba 2 500 m2 podhledových kazet, to je více než 1 200 ks.
- Na celém projektu bylo zpracováno celkem přes 220 tun hliníkových plechů.
- V rámci dodávky opláštění bylo zrealizováno přes 200 tun ocelových konstrukcí, z toho nosná konstrukce kýlu činí zhruba 30 tun.
- Na fasády bylo použito přes 2 600 ks skel různých typů a složení.
- Nainstalované GRC desky a tvarovky (sklovláknobeton) představují téměř 2 500 ks.
- Největší skla mají celkovou tloušťku 80 mm a jejich váha, při výšce zhruba 5 m, přesahuje 1 300 kg.
Při výrobě modulových fasád bylo nezbytné mít veškeré dodávky na jednom místě ve stejném čase, jinak nebylo možné moduly dokončit dle plánovaného postupu a výrobní linka by se zastavila. Nicméně i pro výrobu ostatních konstrukcí byla včasnost a kvalita dodávek rovněž důležitá.
Stejně velký význam mělo také plánování a kompletnost závozů na stavbu pro montáž tak, aby byl zajištěn potřebný postup montáže a využití mechanizace. Při tak velkém objemu a druhovosti zaváženého materiálu, který navíc má na montáži mnohdy jedinečné využití na různých místech objektu, bylo naprosto nezbytné tomuto procesu věnovat velkou pozornost.
Montáž obecně vyžadovala vysoké nároky na primární geodetické vytyčení i rozměření a přesnost samotné realizace. Byla prováděna s využitím stacionárních jeřábů v kombinaci s další mechanizací, tj. mobilních jeřábů a přístupových plošin různých typů.
Konstrukci kýlu lze rozdělit do tří realizačních úrovní
- primární ocelová konstrukce,
- sekundární nosné a rektifikační prvky,
- finální pohledové panely.
Plošiny byly využívány pro osazení všech obloukových a vertikálních lamel (tvarovek) nad kýlem a po jeho bocích, ale také pro montáž obkladů čelních stran na terasách. Částečně se z plošin osazovaly vodorovné tvarovky, které nebylo možné osadit předem ve výrobě. Plošiny rovněž pomáhaly při montáži a opravách na vybraných částech fasád.
Pro osazování některých dílů bylo nutné navrhnout a vyrobit vahadla, bez nichž by některé části nebylo možné instalovat.
Specifická byla také montáž podhledů a obkladů na terasách Rotated Plazza z důvodu vějířovitého konceptu teras. Bylo nezbytné postavit v této části rozsáhlé prostorové lešení, které umožnilo přístup ke kaskádovitě vystupujícím částem teras.
Bez prostorového lešení s opěrnými stabilizujícími věžemi by se neobešla ani montáž na Diagonal Bays.
ZLATÝ KÝL
Dominantou celé stavby a výjimečný svým tvarem je zlatý kýl v průčelí objektu. Konstrukce kýlu má exteriérovou a interiérovou část. Přes prosklenou fasádu, která tyto dvě části odděluje, kýl jako by kontinuálně opticky přechází z exteriérové strany do interiéru. Prostorově zborcené plochy jednotlivých dílů kýlu, jež na sebe navazují, činí každý díl originálem. To znamená, že plocha kýlu neobsahuje shodné pohledové díly.
Koncepce technického řešení kýlu vychází z principu tvarování karoserie automobilů, kde jednotlivé plochy na sebe musí plynule navazovat. Jednotlivé prvky jsou po výrobě standardními postupy nezměřitelné. V našem případě se jedná o zborcené přímkové plochy.
Celý koncept byl od počátku založen na práci s digitálními daty. Přes všechny procesy od zpracování projektové dokumentace přes převod digitálních dat do samotné výroby a s následným využitím při montáži, s plnou důvěrou, že výrobek a hotová fasáda budou odpovídat digitálnímu modelu.
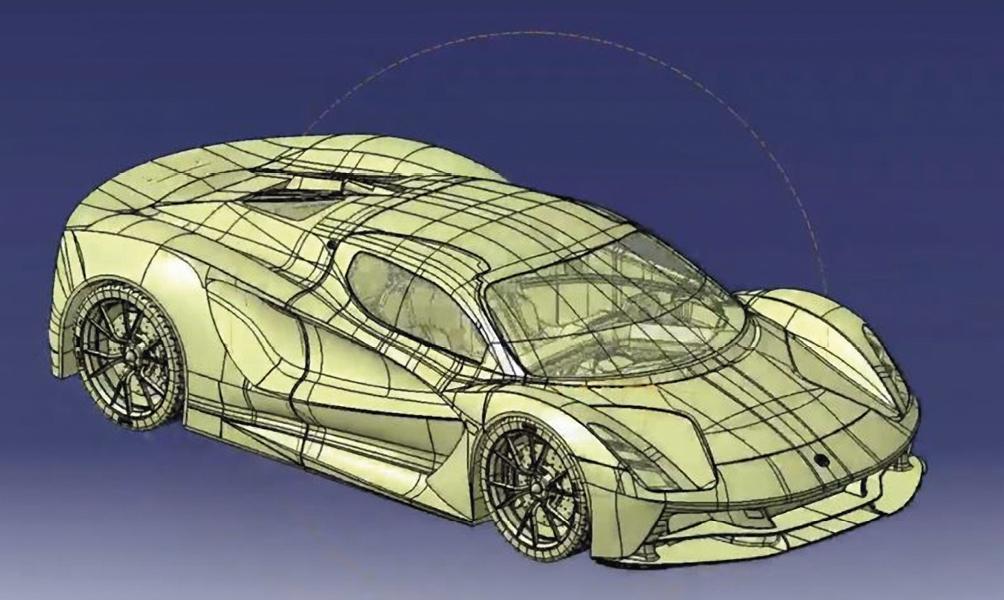
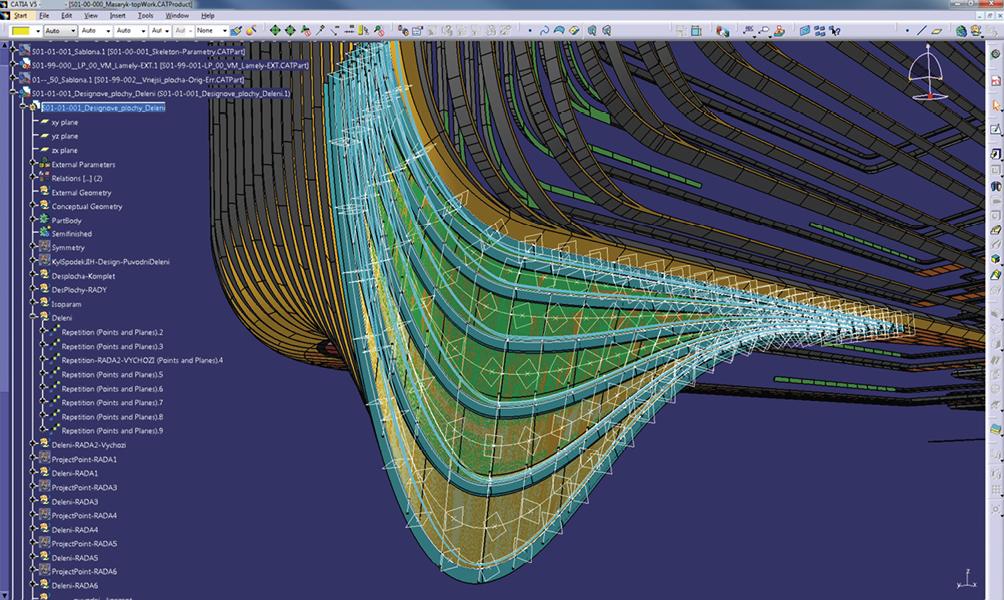
Pro ověření geometrie výsledného výrobku a porovnání s výchozím 3D modelem bylo použito v některých případech 3D skenování, díky němuž je možné vyhodnotit případné odchylky.
Náročným procesem modelování a vyhodnocování výsledných tvarů a návazností procházely nejen samotné pohledové panely kýlu, ale všechny jednotlivé prvky, ze kterých se konstrukce kýlu skládá.
Primární nosná ocelová konstrukce je tvořena kombinací rovných a ohýbaných trubek, jež odpovídají tvaru finálního kýlu. Konstrukce je kotvena do betonového skeletu. Už výroba a montáž této konstrukce vyžadovaly vysokou přesnost a nadstandardní přístup ke zpracování dokumentace.
Sekundární nosné a rektifikační prvky zajišťují kotvení pohledových panelů k nosné primární ocelové konstrukci. Pro tuto část byl vyvinut speciální prvek, tzv. Spider (pavouk), nastavitelný ve všech směrech tak, aby bylo možné eliminovat výrobní a montážní tolerance, rektifikovat a ustavit velmi přesně pohledové panely do požadované polohy. Spider je přes objímku s kulovým čepem osazen na trubkovou konstrukci. Z kulového čepu pak vycházejí vzájemně propojená nastavitelná ramena, přes která je výsledně přikotven pohledový panel.
Spider zajišťuje přesné osazení panelu a jeho zafixování v požadované poloze. Zatížení od samotného panelu pak přenáší síť nerezových lanek s napínáky, která jsou rovněž kotvená k trubkové konstrukci.
Pro přesné ustavení Spiderů byla nutná stálá přítomnost geodetů, kteří vyměřovali jednotlivé pozice, ale také opakovaně kontrolovali pozici každého Spideru i v průběhu následné montáže.
Pro co nejpřesnější geodetické zaměření v prostoru byly pro každý Spider na 3D tiskárně vytisknuty unikátní plastové nástavce. Pro usnadnění vytyčení každé jednotlivé polohy byly použity kloubové stativy osazené na konstrukci.
Celkem bylo užito více než 400 ks těchto Spiderů, jež měly sice stejný technický princip, avšak lišily se polohou objímky a délkou ramen v závislosti na své pozici v konstrukci. Výše uvedený princip Spiderů a jejich přesnost vytyčení byla klíčová vzhledem k tomu, že po namontování jednotlivých panelů již nebyla geodetická kontrola možná.
Finální pohledová plocha kýlu je vyskládána z unikátních designových panelů. Pro maximální zachování tvarů a zefektivnění celého procesu byly datové formáty vytvořené ve 3D modelu následně transformovány do výroby.
Výroba začínala u vypálených základních rámů laserem, respektive jejich jednotlivých žeber, které se následně sestavovaly systémem podobným jako puzzle.
Rám, který vytvářel základní tvar každého panelu, byl „potažen“ zlatým eloxovaným plechem, jenž se přizpůsobil požadovanému tvaru příslušného rámu a následně byl ve své poloze ke konstrukci zafixován.
Probíhaly ještě další procesy a operace ve výrobě, jako například doplnění dalších fixačních bodů pro doladění výsledného tvaru plechu, opatření lemů, doplnění montážních prvků nebo kontrola povrchů.
Jednotlivé panely měly jasně stanovenou posloupnost montáže. Osazení panelů na předem ustavené Spidery probíhalo pomocí plošin a zvedacích prostředků. Vyrovnání každého panelu do výsledné pozice se opět neobešlo bez přesné práce geodetů.
Návrh a výrobní dokumentace byly kompletně zpracovávány v systému CATIA, v němž bylo možné pracovat s objemnými daty a převádět obecné plochy do rozvinutelných tvarů. Byly vytvořeny obsáhlé parametrické modely s desítkami měnitelných parametrů a pomocná makra pro zpracování výsledného 3D modelu.
I přes maximální snahu o zjednodušení dokumentace pro výrobu designových panelů bylo vytvořeno více než 18 000 výrobních a kompletačních výkresů.
ZÁVĚREM
Sipral si váží příležitosti podílet se na realizaci takto výjimečného projektu. Od počátku jsme si všichni byli vědomi náročnosti celého projektu, avšak realizace v některých ohledech předčila očekávání.
Díky velkému nasazení všech, kteří se na realizaci obvodového pláště podíleli, včetně subdodavatelů, odvaze a odhodlání přijmout určité riziko i vstřícnému přístupu k řešení někdy až téměř nerealizovatelných požadavků se podařilo obvodový plášť dokončit do současné podoby. Nyní budou ještě probíhat opravy či výměny poškozených dílů a odstraňování vad.
V průběhu realizace bylo nutné operativně řešit mnoho situací a také upravovat postupy i průběh montáží s ohledem na vývoj a testování některých částí fasády. Korigovat tedy také práce na plášť navazujících profesí. Bez konstruktivního přístupu klienta a stavebního manažera a vnímání komplexnosti celé fasády by to nebylo možné.
Autoři:
Martin Binovec, provozní ředitel ve společnosti Sipral.
Ing. David Baltaretu, manažer projektu Masaryčka ve společnosti Sipral.